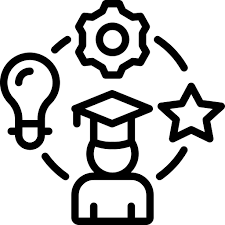
edn
EDN.com is a leading online resource that caters to the electronics engineering community, providing a wealth of information on technology trends, design techniques, and industry news. With a deep-rooted history dating back to 1956, EDN.com continues to serve as a reliable source of insight and education for electrical engineers, systems designers, and professionals in the electronics field. The website covers a wide range of topics, including analog and digital design, embedded systems, power management, test and measurement, and emerging technologies. EDN.com aims to empower engineers with the knowledge and tools they need to stay ahead in the rapidly evolving world of electronics.
-
EncryptedSite is Encrypted
-
CountryHosted in United States
-
CitySan Antonio, Texas
-
Latitude\Longitude29.4247 / -98.4935 Google Map
-
Traffic rank#21,254 Site Rank
-
Site age27 yrs old
-
Site Owner informationWhois info
Website is Safe
Site is not blacklisted
Traffic rank
#21,254
#21,254
Site age
27 yrs
27 yrs
Location
United States
United States
Popular Questions for edn
Newest job postings for edn
via Jora
posted_at: 21 days agoschedule_type: Full-time
At BASF, we create chemistry through the power of connected minds. By balancing economic success with environmental protection and social responsibility, we are building a more sustainable future through chemistry. As the world’s leading chemical company, we help our customers in nearly every industry meet the current and future needs of society through science and innovation.
We provide a challenging and rewarding work environment with a strong
At BASF, we create chemistry through the power of connected minds. By balancing economic success with environmental protection and social responsibility, we are building a more sustainable future through chemistry. As the world’s leading chemical company, we help our customers in nearly every industry meet the current and future needs of society through science and innovation.
We provide a challenging and rewarding work environment with a strong emphasis on process safety, as well as the safety of our employees and the communities we operate in and are always working to form the best team—especially from within, through an emphasis on lifelong learning and development.
And we are constantly striving to become an even better place to work. BASF has been recognized by Forbes Magazine as one of America’s Best Large Employers in 2021. Come join us on our journey to create solutions for a sustainable future!
Where the Chemistry Happens......
Quality and CI Manager- Chattanooga... TN
This dual role provides the unique opportunity for an individual to utilize a variety of skills and experience in managing the Quality, Continuous Improvement, and Operational Excellence (OPEX). The successful candidate will provide leadership to the Quality Control Laboratory team, maintain documentation to verify compliance with ISO/Quality, OPEX, and lead the Site team in continuous improvement activities.
Duties:
• Continuous Improvement - Lead, coach and/or facilitate Continuous Improvement projects. Identify & select continuous improvement projects, set targets and track results. Manage and execute Lean Six Sigma training programs. Lead continuous improvement workshops and kaizen events. Provide process improvement and variation reduction expertise as required.
• Quality Control Lab Leadership – Manage Quality Supervisor and laboratory technicians to ensure products meet customer requirements.
• Management Systems – Ensure site compliance with ISO standards and other regulatory requirements (e.g., RCMS). Manage nonconformance system to ensure customer response in a timely manner and corrective action to eliminate issues.
• OpEx – Lead development and execution of 4-year Operational Excellence plan.
• Function as QA laboratory manager to manage the QA laboratories using goals/objectives, training and procedures to ensure that lab personnel successfully implement the ISO quality management system, thus ensuring shipment of quality product.
• Function as the Site ISO Quality Management System Coordinator to manage the ISO 9000 quality system by 1) establishing clear, aggressive goals and objectives that drive the quality process performance to ensure continued ISO certification, 2) to manage the ISO 9000 internal auditing process to ensure continued ISO certification, 3) to manage the customer NCM (nonconformance maintenance) system, using the SAP Y1 and Y6 NCM process and appropriate measurements to ensure that customer complaints are addressed with suitable root causes and effective corrective actions and 4) to manage the customer NCM (nonconformance maintenance) system to establish, manage, and communicate key quality process metrics that monitor and improve plant processes and involve all employees in the total quality effort.
• Serve as a quality representative to the CSLT using site goals and the Management Review process to continually improve site processes.
• Manage continuous improvement, corrective action, and problem solving activities to identify quality issues and opportunities for improvement of the quality system through effective Corrective Action/Preventive Action plans.
• Implement quality control and quality assessment processes in the QA lab through procedures, training and coaching to ensure that instruments used for monitoring the quality of the product controlled and prevent nonconforming product from being shipped to the customer.
• Supervise the analysis of raw materials, intermediate products, finished products and other chemical samples according to established specifications to ensure quality and availability of final product
• Establish and maintain procedures and work instructions that support the Quality Management system
• Effectively implement software tools such as IQS Proficient, SAP, Microsoft Office Programs, etc. which enhance quality reporting
• Ensure the suitability of laboratory equipment through proper operation, maintenance, calibration, verification and good quality control and assessment activities
• Identify training opportunities; implement goals/objectives to develop employee knowledge, skills and talents leading employees to better personal and professional fulfillment and participation in the quality process.
• Budget and control laboratory expenses, travel expenses, fixed costs, etc., within goals set by the Leadership Team
• Function as the Site ISO Quality Management System Coordinator to manage the ISO quality system by establishing clear, aggressive goals and objectives that drive quality performance to ensure continued ISO certification
• Lead the ISO internal audit teams at the Chattanooga site to perform effective internal audits which will enhance our ability to maintain our external certification
• Participate in the EDN quality system as a Lead internal auditor to perform effective internal audits at other EDN sites which enhance their ability to maintain external certification
• Perform yearly management review meetings to review quality data, formulate goals and action items to achieve goals which demonstrate continuous improvement in our processes
• Manage the closure of all quality/RCMS audit findings to ensure closure in a timely manner with effective corrective actions
• Use the SAP NCM system to manage internal and external nonconformances leading to effective root causes and corrective actions and improvements in meeting customer requirements and a reduction of Cost of Poor Quality
• Determine QUIZ and COPQ (Cost of Poor Quality) and set goals to reduce COPQ
• Use Y1 and Y6 - NCM data, Internal and External Audit findings and CAPAs to set quality goals to improve processes and reduce nonconformances
• Generate quality data and significant statistical data to support plant personnel in their efforts to enhance process control, meet customer requirements and continuously improve our product quality characteristics
• Manage the plant quality-related continuous improvement projects by setting goals and KPIs that drive continuous improvement of plant processes
• Provide technical support for sales, marketing R&D, Production and other BASF units/departments by providing quality data, statistical information and technical expertise for raw material evaluations, process improvements, new product development and expanded analytical capability
• Provide SPC charts to internal and external customers
• Lead the Operational Excellence Team process to implement ideas and suggestions which improve safety, product quality and plant operations Show more details...
We provide a challenging and rewarding work environment with a strong emphasis on process safety, as well as the safety of our employees and the communities we operate in and are always working to form the best team—especially from within, through an emphasis on lifelong learning and development.
And we are constantly striving to become an even better place to work. BASF has been recognized by Forbes Magazine as one of America’s Best Large Employers in 2021. Come join us on our journey to create solutions for a sustainable future!
Where the Chemistry Happens......
Quality and CI Manager- Chattanooga... TN
This dual role provides the unique opportunity for an individual to utilize a variety of skills and experience in managing the Quality, Continuous Improvement, and Operational Excellence (OPEX). The successful candidate will provide leadership to the Quality Control Laboratory team, maintain documentation to verify compliance with ISO/Quality, OPEX, and lead the Site team in continuous improvement activities.
Duties:
• Continuous Improvement - Lead, coach and/or facilitate Continuous Improvement projects. Identify & select continuous improvement projects, set targets and track results. Manage and execute Lean Six Sigma training programs. Lead continuous improvement workshops and kaizen events. Provide process improvement and variation reduction expertise as required.
• Quality Control Lab Leadership – Manage Quality Supervisor and laboratory technicians to ensure products meet customer requirements.
• Management Systems – Ensure site compliance with ISO standards and other regulatory requirements (e.g., RCMS). Manage nonconformance system to ensure customer response in a timely manner and corrective action to eliminate issues.
• OpEx – Lead development and execution of 4-year Operational Excellence plan.
• Function as QA laboratory manager to manage the QA laboratories using goals/objectives, training and procedures to ensure that lab personnel successfully implement the ISO quality management system, thus ensuring shipment of quality product.
• Function as the Site ISO Quality Management System Coordinator to manage the ISO 9000 quality system by 1) establishing clear, aggressive goals and objectives that drive the quality process performance to ensure continued ISO certification, 2) to manage the ISO 9000 internal auditing process to ensure continued ISO certification, 3) to manage the customer NCM (nonconformance maintenance) system, using the SAP Y1 and Y6 NCM process and appropriate measurements to ensure that customer complaints are addressed with suitable root causes and effective corrective actions and 4) to manage the customer NCM (nonconformance maintenance) system to establish, manage, and communicate key quality process metrics that monitor and improve plant processes and involve all employees in the total quality effort.
• Serve as a quality representative to the CSLT using site goals and the Management Review process to continually improve site processes.
• Manage continuous improvement, corrective action, and problem solving activities to identify quality issues and opportunities for improvement of the quality system through effective Corrective Action/Preventive Action plans.
• Implement quality control and quality assessment processes in the QA lab through procedures, training and coaching to ensure that instruments used for monitoring the quality of the product controlled and prevent nonconforming product from being shipped to the customer.
• Supervise the analysis of raw materials, intermediate products, finished products and other chemical samples according to established specifications to ensure quality and availability of final product
• Establish and maintain procedures and work instructions that support the Quality Management system
• Effectively implement software tools such as IQS Proficient, SAP, Microsoft Office Programs, etc. which enhance quality reporting
• Ensure the suitability of laboratory equipment through proper operation, maintenance, calibration, verification and good quality control and assessment activities
• Identify training opportunities; implement goals/objectives to develop employee knowledge, skills and talents leading employees to better personal and professional fulfillment and participation in the quality process.
• Budget and control laboratory expenses, travel expenses, fixed costs, etc., within goals set by the Leadership Team
• Function as the Site ISO Quality Management System Coordinator to manage the ISO quality system by establishing clear, aggressive goals and objectives that drive quality performance to ensure continued ISO certification
• Lead the ISO internal audit teams at the Chattanooga site to perform effective internal audits which will enhance our ability to maintain our external certification
• Participate in the EDN quality system as a Lead internal auditor to perform effective internal audits at other EDN sites which enhance their ability to maintain external certification
• Perform yearly management review meetings to review quality data, formulate goals and action items to achieve goals which demonstrate continuous improvement in our processes
• Manage the closure of all quality/RCMS audit findings to ensure closure in a timely manner with effective corrective actions
• Use the SAP NCM system to manage internal and external nonconformances leading to effective root causes and corrective actions and improvements in meeting customer requirements and a reduction of Cost of Poor Quality
• Determine QUIZ and COPQ (Cost of Poor Quality) and set goals to reduce COPQ
• Use Y1 and Y6 - NCM data, Internal and External Audit findings and CAPAs to set quality goals to improve processes and reduce nonconformances
• Generate quality data and significant statistical data to support plant personnel in their efforts to enhance process control, meet customer requirements and continuously improve our product quality characteristics
• Manage the plant quality-related continuous improvement projects by setting goals and KPIs that drive continuous improvement of plant processes
• Provide technical support for sales, marketing R&D, Production and other BASF units/departments by providing quality data, statistical information and technical expertise for raw material evaluations, process improvements, new product development and expanded analytical capability
• Provide SPC charts to internal and external customers
• Lead the Operational Excellence Team process to implement ideas and suggestions which improve safety, product quality and plant operations Show more details...
Search trends for edn